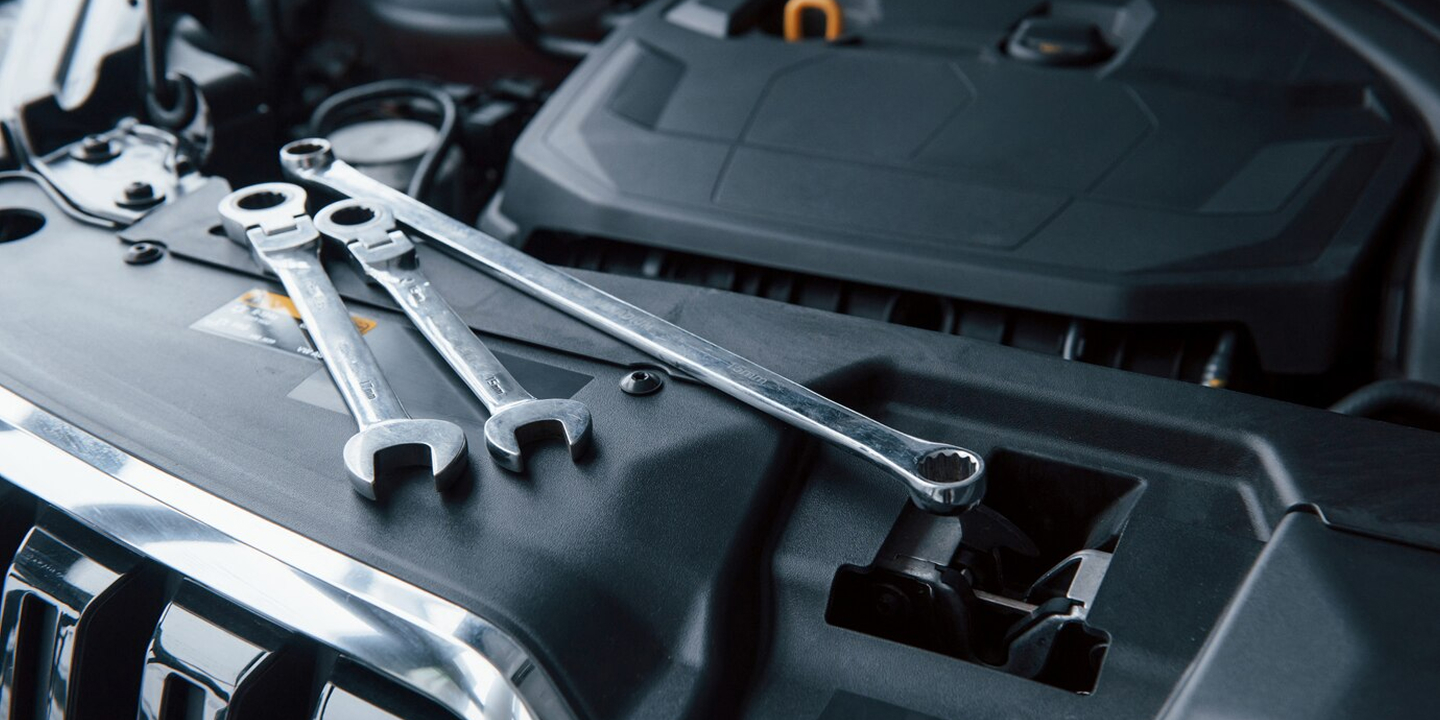
[ Products ]
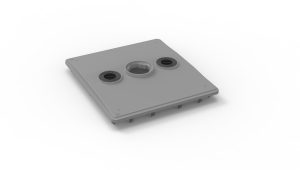
Grommet Battery Lid Type 3
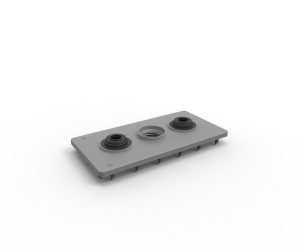
Grommet Battery Lid Type 2
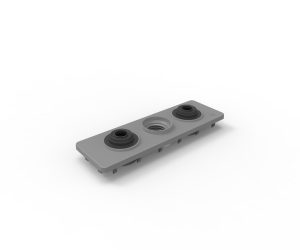
Grommet Battery Lid Type1
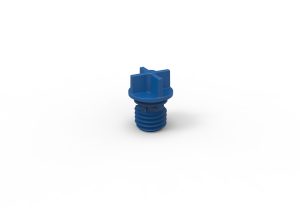
EV Plug
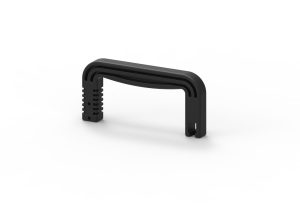
Battery Lid Handle Type 4
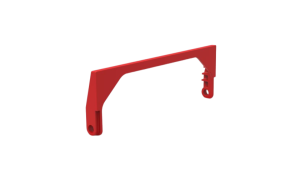
Battery Lid Handle Type 3
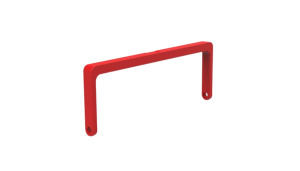
Battery Lid Handle Type 2
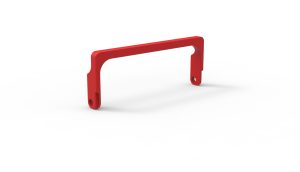
Battery Lid Handle Type 1
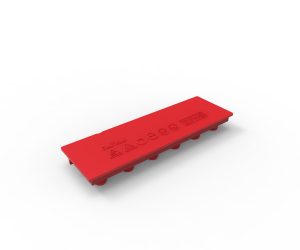
Battery Lid Cover Type 2
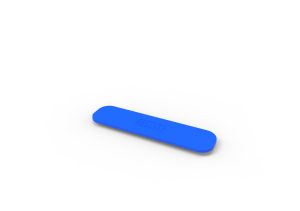
Battery Lid Cover Type 1
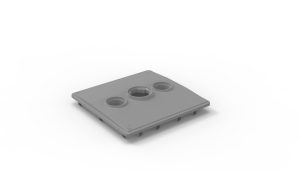
Battery Lid Type 11
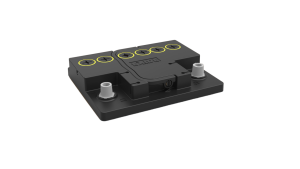
Battery Lid Type 10
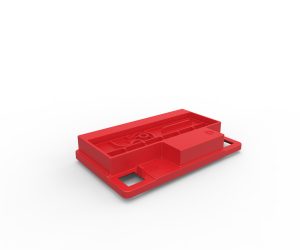
Battery Lid Type 9
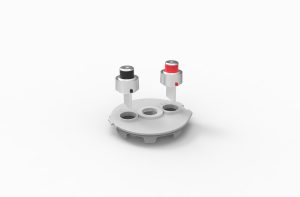
Battery Lid Type 8
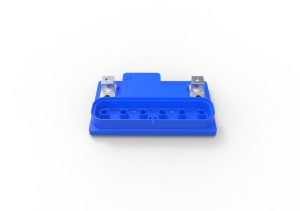
Battery Lid Type 7
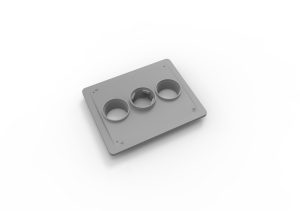
Battery Lid Type 6
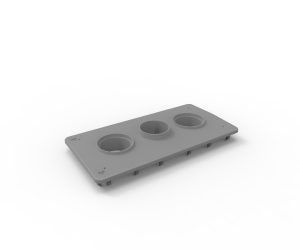
Battery Lid Type 5
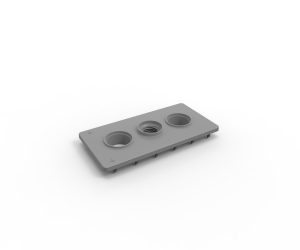
Battery Lid Type 4
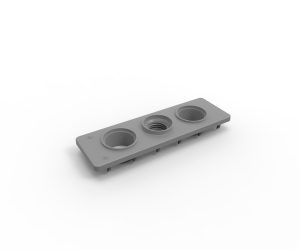
Battery Lid Type 3
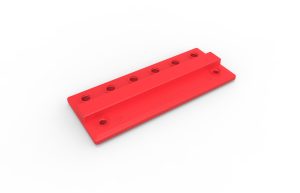
Battery Lid Type 2
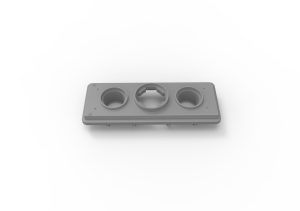
Battery Lid Type 1
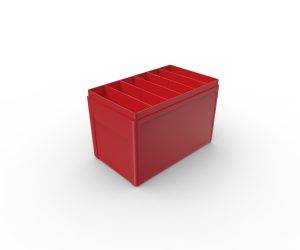
Battery Container Type 2
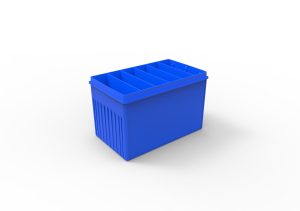
Battery Container Type 1
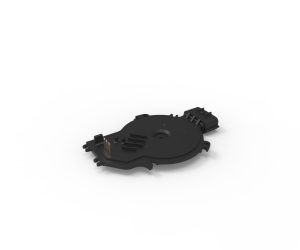
Gear Box Cover Type 4
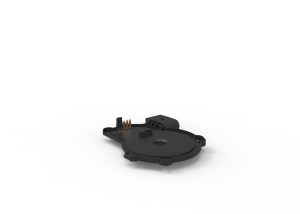
Gear Box Cover Type 3
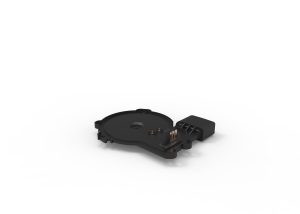
Gear Box Cover Type 2
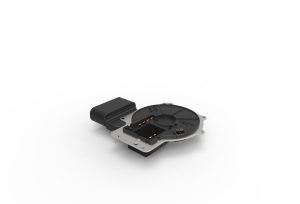
Gear Box Cover Type 1
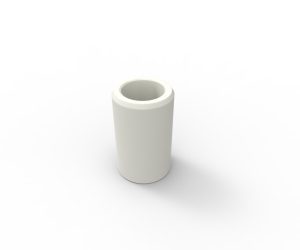
Bush Type 2
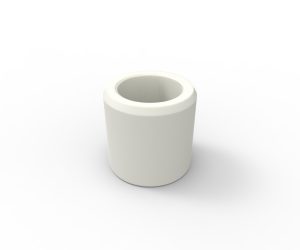
Bush Type 1
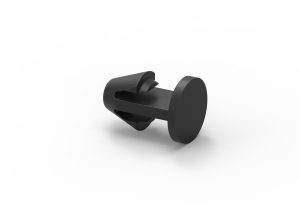
Snap Locker
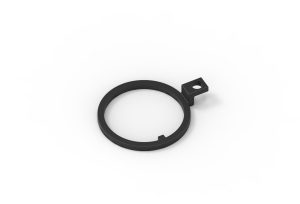
Seal Cap Locker
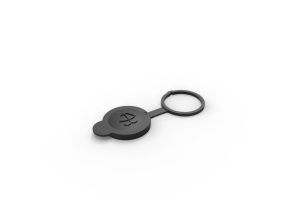
Seal Cap
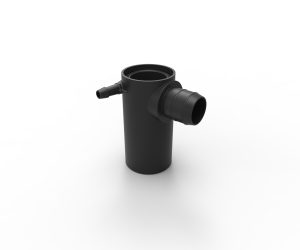
Pump Housing
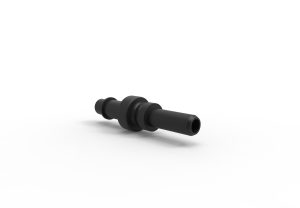
Plastic Joint
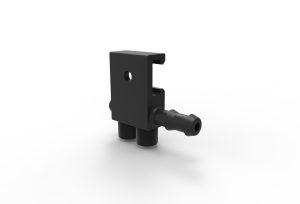
Nozzle
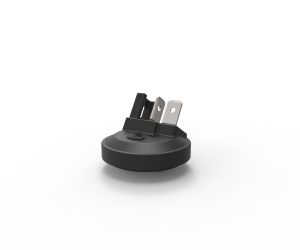
Insert Moulded Housing Cap
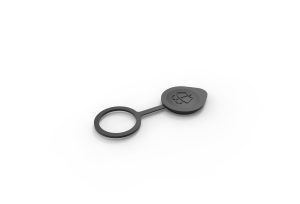
Intel Cap
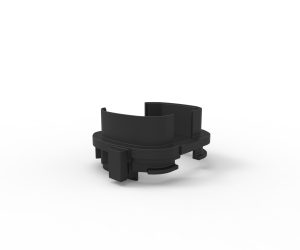
Top Core Cover Type 2
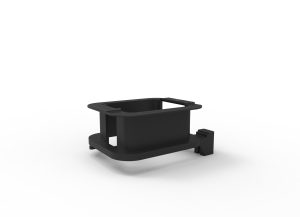
Top Core Cover Type 1
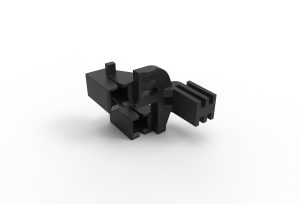
Terminal Holder
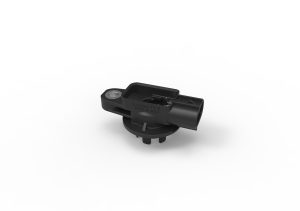
Stick Coil
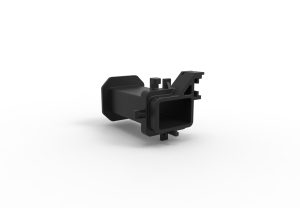
Primary Bobbing
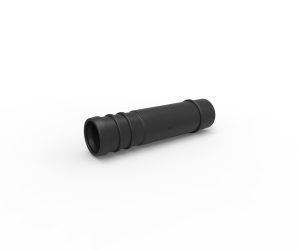
Pole Joint
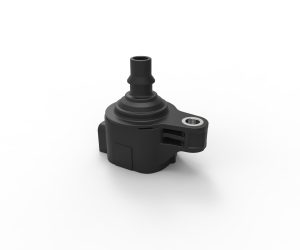
Outer Case Coil Type 2
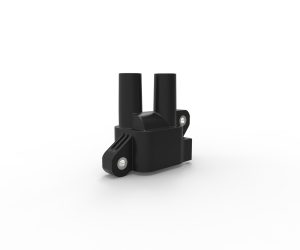
Outer Case Coil Type 1
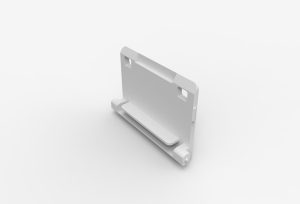
Switch Gear Type 5

Switch Gear Type 4
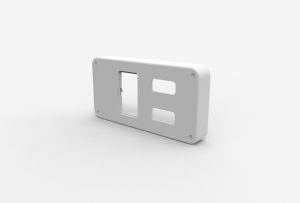
Switch Gear Type 3
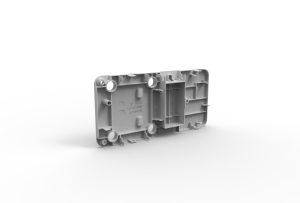
Switch Gear Type 2
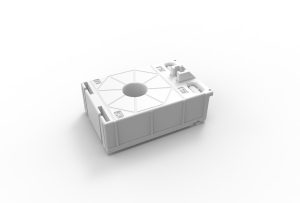
Switch Gear Type 1
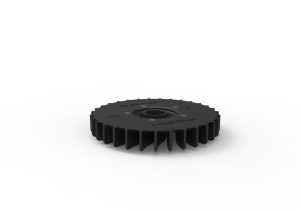
Fan Blade Type 5
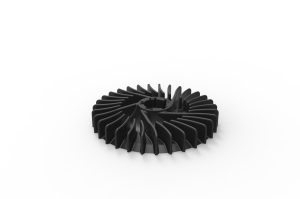
Fan Blade Type 4
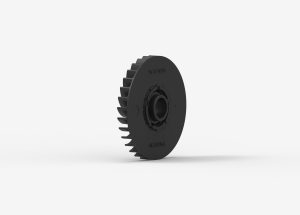
Fan Blade Type 3
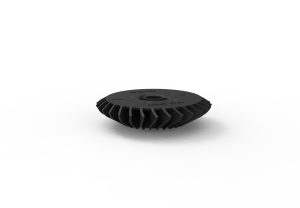
Fan Blade Type 2
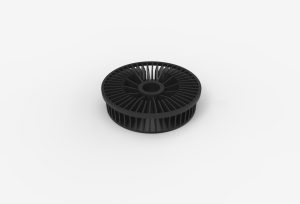
Fan Blade Type 1
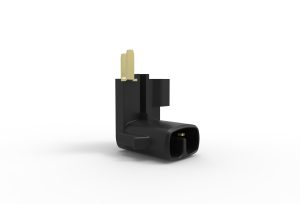
Coupler Type 3
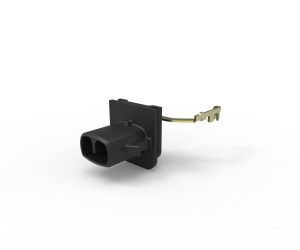
Coupler Type 2
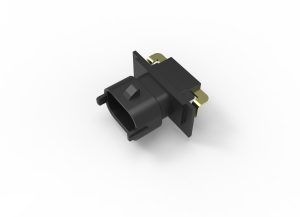
Coupler Type 1
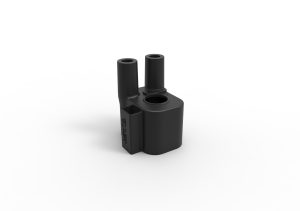
Case Coil Type 3
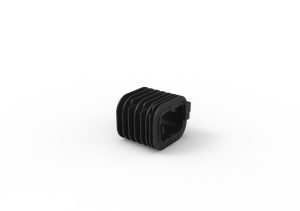
Bobbing
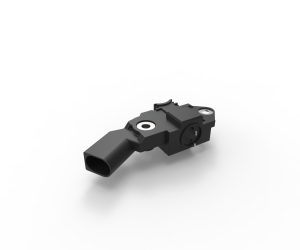
Regulator Type 2
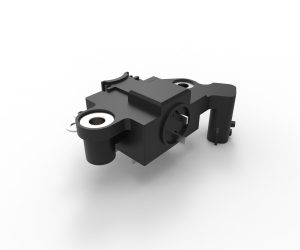
Regulator Type 1
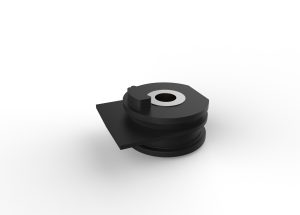
Positive terminal bush
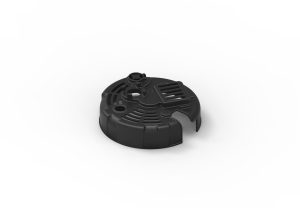
Rear cover Type 2
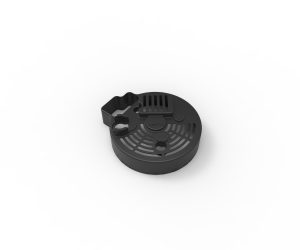
Rear cover Type 1
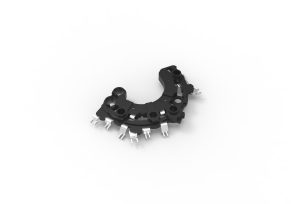
Field Moulding Type 3
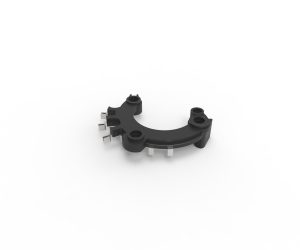
Field Moulding Type 2
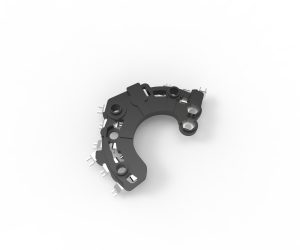